The construction industry is at the crossroads of climate urgency and economic performance. As governments, developers, and investors align with net-zero targets, the pressure to deliver low-carbon, cost-effective buildings is imperative. Amidst this transformation, one tool stands out as a bridge between financial intelligence and environmental stewardship: Life Cycle Cost Analysis (LCCA).
While most are familiar with LCCA’s role in forecasting long-term costs, fewer understand its profound potential in driving decarbonisation strategies. By shifting focus from just upfront expenditures to total cost and impact across an asset’s life span, LCCA empowers the construction sector to make choices that minimise both emissions and waste.
In a world where 40% of global carbon emissions are linked to the built environment, a clear understanding of life cycle analysis and carbon data, and how it intersects with costs can be the difference between a greenwashed effort and true climate leadership.
This article explores how life cycle cost analysis in construction not only optimises budgets, but actively reduces embodied and operational carbon—making it a linchpin for sustainable development. We’ll also explore key tools, real-world examples, and practical advice on applying LCCA to meet both financial and environmental goals.
What Is Life Cycle Cost Analysis in Construction?
Life Cycle Cost Analysis (LCCA) is a structured method for evaluating the total cost of an asset across its full operational life. This covers not only the initial design and build phase but also ongoing maintenance, energy usage, repairs, and eventual decommissioning.
In construction, LCCA helps identify which systems, materials, and technologies offer the best long-term value. More importantly, it enables decision-makers to weigh costs against carbon impact. For instance, a high-efficiency HVAC system might involve higher upfront costs but can substantially reduce both utility bills and CO₂ emissions over a 20 to 30-year lifespan.
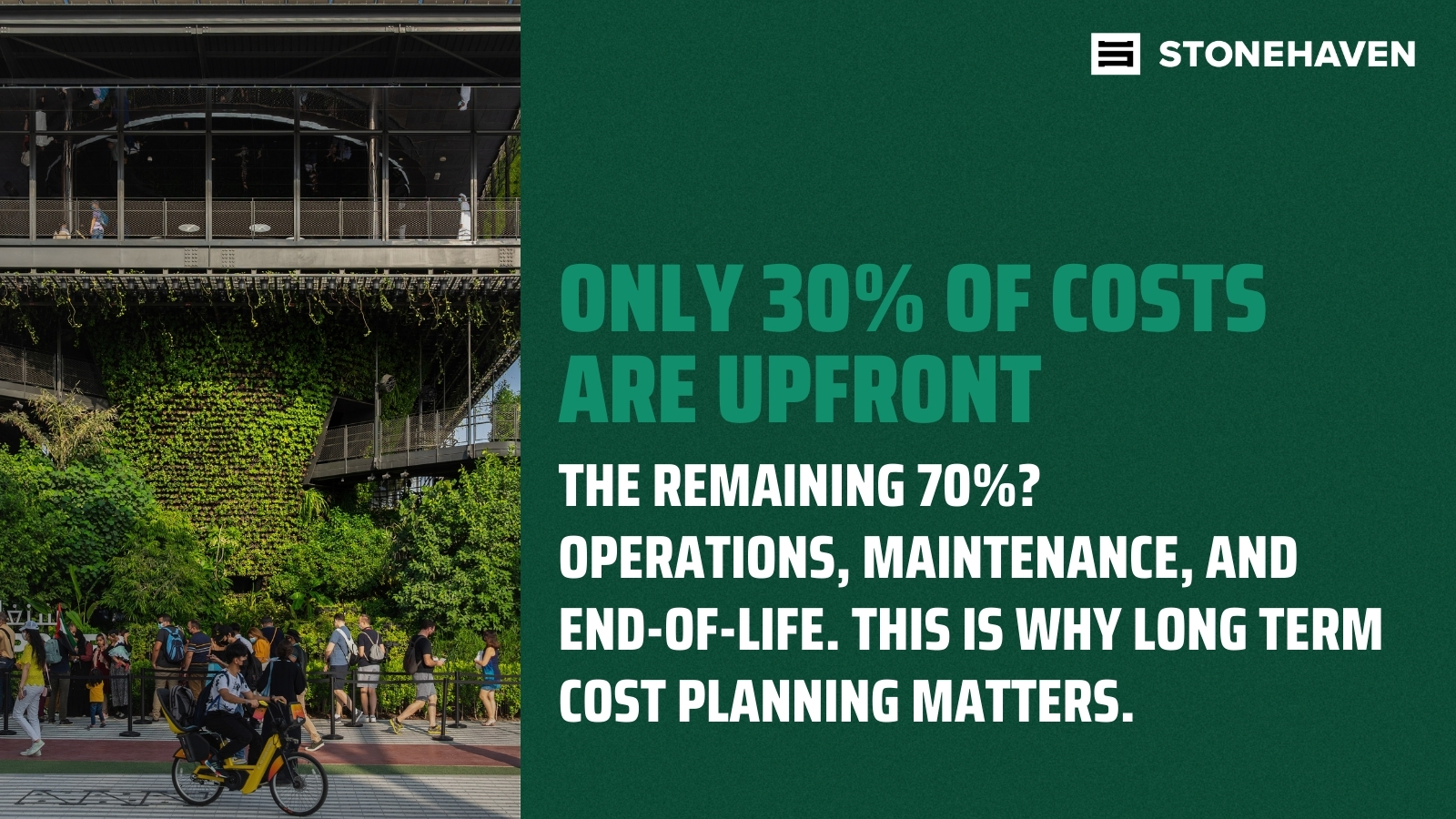
LCCA typically includes the following cost categories:
● Initial capital cost (procurement, construction)
● Operating costs (energy, water, staffing)
● Maintenance and repair costs
● Replacement costs
● End-of-life/disposal costs
To adjust for time, LCCA uses a discount rate to calculate the present value of future expenses. When combined with carbon life cycle analysis, this approach becomes a comprehensive strategy that balances financial prudence with environmental responsibility.
For context, initial construction costs usually account for only 25% to 35% of a building's total lifecycle cost, while the remaining 65% to 75% arises from operations, maintenance, and end-of-life expenses. Furthermore, the construction and manufacturing sectors contribute approximately 57% of global carbon emissions, underscoring the significant environmental footprint of the built environment.
Increasingly, life cycle cost analysis software now integrates carbon metrics alongside cost, enabling deeper insight into how material choices and design decisions affect overall sustainability. This holistic view is essential in meeting regulatory frameworks and ESG commitments.
How to Conduct Life Cycle Cost Analysis for Carbon Reduction
Incorporating decarbonisation objectives into WLCC means evaluating not just how much a system costs, but how much carbon it emits across its life span. Here's how construction professionals can structure an LCCA process that aligns with climate goals:
1. Define the Scope with Carbon in Mind
Start by defining project boundaries. Will you assess the entire building, or only major carbon-intensive components like cladding, MEP systems, or concrete structure?
Include:
● Embodied carbon (from materials manufacturing and transport)
● Operational carbon (from energy consumption)
● End-of-life carbon (from demolition or reuse)
2. Collect and Standardise Cost & Carbon Data
Use tools and databases like:
● RICS Whole Life Carbon Assessment
● HM Treasury’s Green Book
● LCA software such as One Click LCA or eTool
Gather data in consistent units — AED/kgCO₂e and AED/year — for both cost and carbon comparisons.
3. Model Alternatives
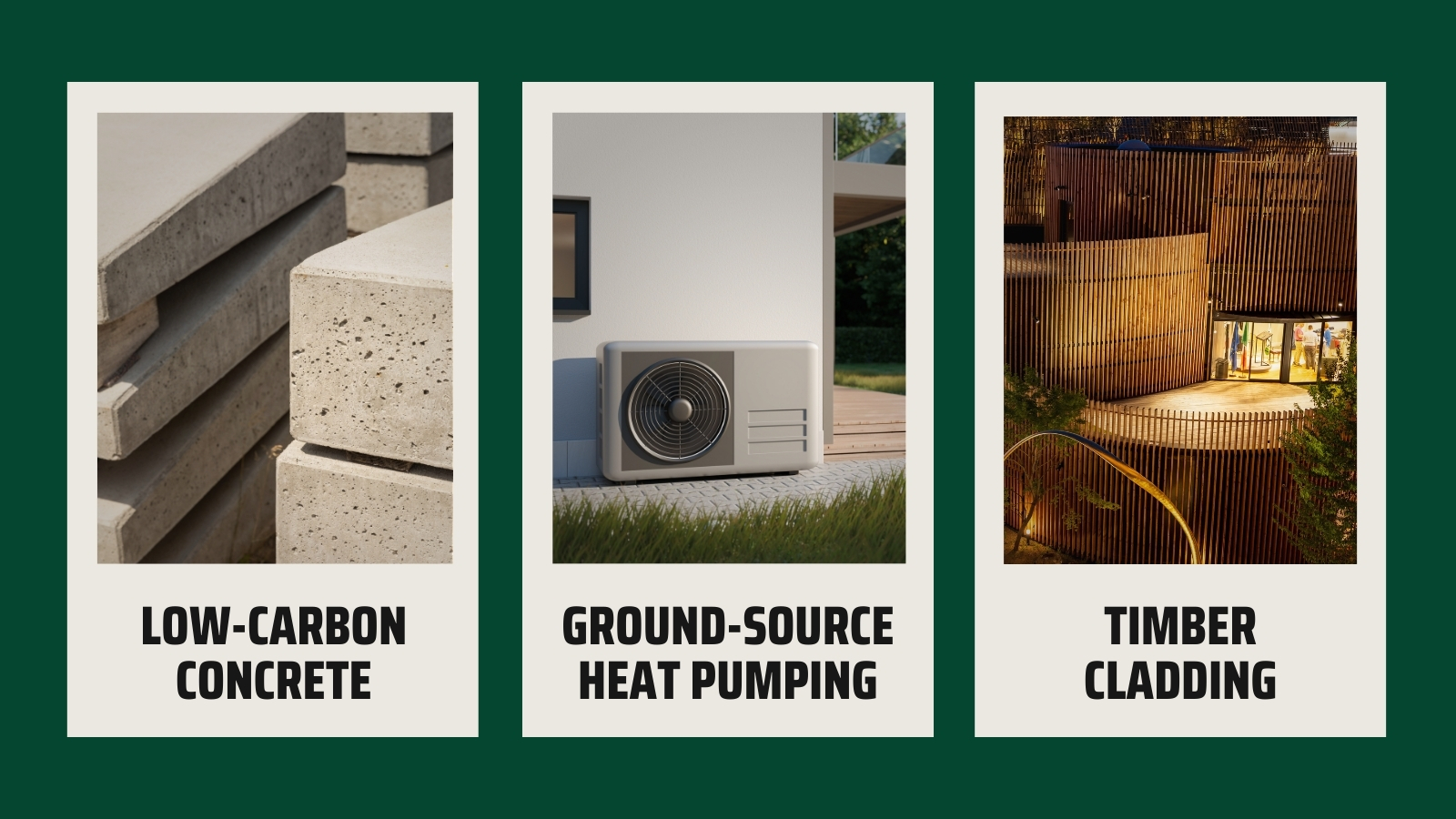
Compare different materials or systems. For example:
● Traditional concrete vs. low-carbon concrete
● Gas boiler vs. ground-source heat pump
● Aluminium facade vs. timber cladding
Each has a distinct carbon and cost profile over time.
4. Apply Discounting
Use a discount rate that is adjusted to inflation volatility to evaluate the present value of future costs and emissions. This ensures fair comparisons and reflects true long-term savings.
5. Optimise for Net Zero
Select the alternative that achieves the lowest combined life cycle cost and carbon emissions. Use shadow pricing of carbon where applicable to monetise environmental impact.
By integrating cost and carbon in a unified model, LCCA becomes a proactive tool to make environmentally responsible decisions economically viable.
Life Cycle Cost Optimisation: How to Maximise Value & Minimise Emissions
Carbon-aware construction starts at the drawing board. With LCCA embedded early in the design phase, architects and engineers can evaluate how decisions made today will influence carbon and cost decades from now.
1. Design for Durability
Materials with longer lifespans and lower maintenance requirements typically offer better LCCA outcomes and lower carbon impact. Timber, for example, offers both carbon sequestration and reduced lifecycle emissions versus steel or concrete.
2. Minimise Operational Emissions
Energy-efficient designs may involve upfront premiums, but LCCA shows their payoff. LED lighting, high-performance glazing, and passive ventilation reduce long-term utility bills and CO₂ output.
3. Prioritise Renewable Technologies
Solar PV, geothermal systems, and air-source heat pumps may appear expensive initially, but LCCA reveals dramatic savings over time, especially when energy prices rise.
4. De-risk Through Modelling
Using life cycle cost analysis teams can model “what if” scenarios. This reveals the sensitivity of both cost and carbon to changes in design assumptions or future energy tariffs.
5. Align with Green Certifications
Tools like BREEAM, LEED, and Estidama require LCCA data for top-tier ratings. Incorporating carbon as a performance metric positions projects to achieve higher certification levels and regulatory compliance.
Ultimately, LCCA enables carbon-conscious design by reframing cost conversations. Instead of asking, “How much does this cost today?” LCCA asks, “What’s the long-term value for people, planet, and profit?”
Benefits of Using Life Cycle Cost Analysis for Decarbonisation
When used as a decarbonisation strategy, life cycle cost analysis (LCCA) offers powerful advantages for stakeholders at every level of the built environment.
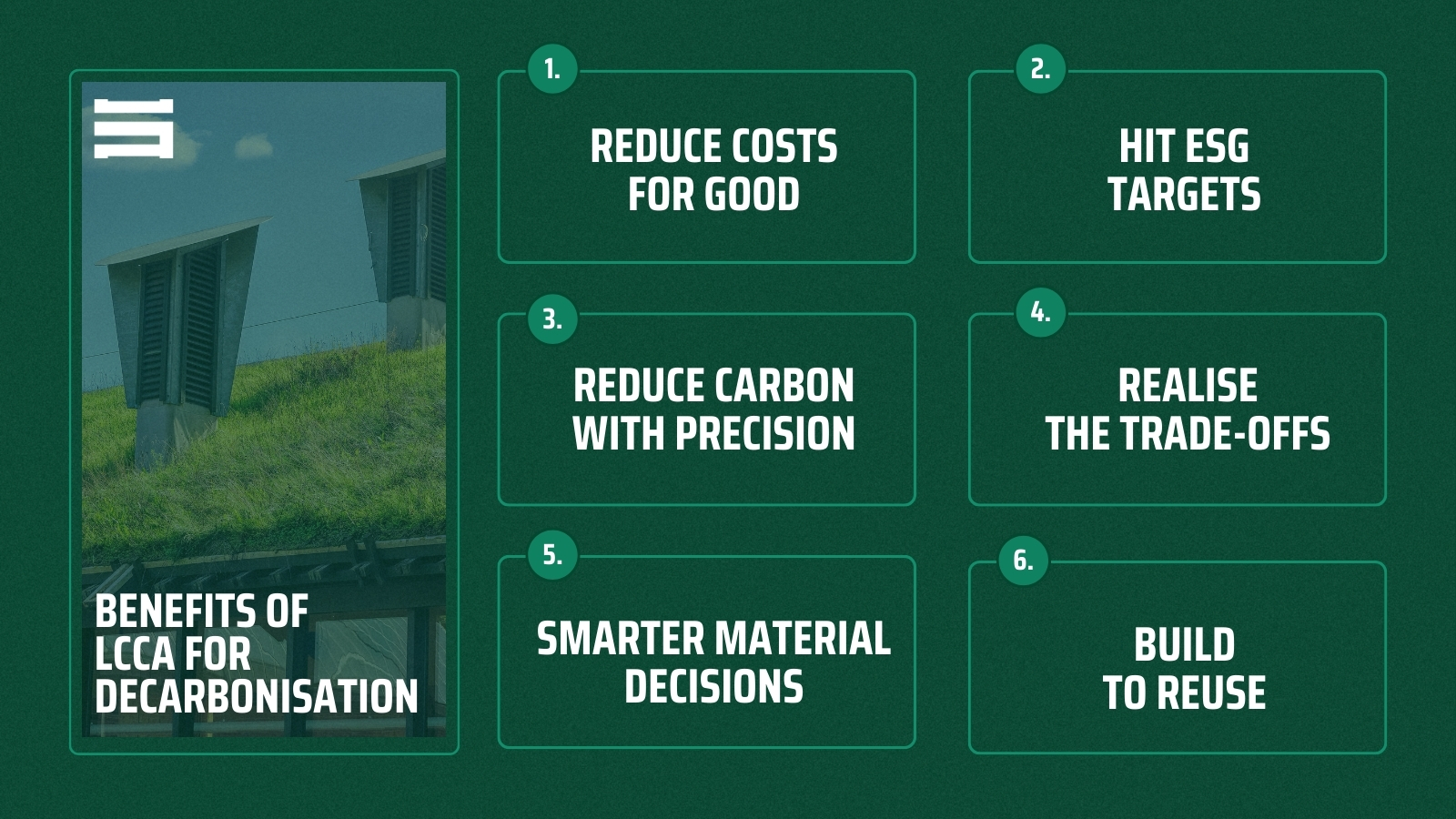
Reduce Costs For Good
LCCA can reduce your long-term energy and maintenance bills. Sustainable choices stop being risky and they start making sense.
Hit ESG Targets and Win Trust
With carbon life cycle data built in, LCCA keeps you on track for environmental KPIs and unlocks access to green financing.
Reduce Carbon with Precision
LCCA gives you a measurable roadmap to net zero, one that balances cost, performance, and emissions.
Know the Trade-Offs
When budgets tighten, LCCA shows what’s really worth keeping. It protects what matters most in sustainability, efficiency, and value.
Make Smarter Decisions
Start with LCCA and every move gets sharper from material selection to facade design. Strategy meets sustainability.
Build to Reuse
LCCA brings the circular economy to life. It rewards modular thinking, reuse, and materials that perform beyond their first life.
In short, life cycle cost analysis in construction is not just a smarter budgeting tool. It is a critical approach for building responsibly and preparing for a low-carbon future.
Solutions for the Challenges in Life Cycle Cost Analysis For Decarbonisation
1. The data isn’t broken, it’s just not regionalised enough
A common misconception is that the data for life cycle costing and carbon modelling simply doesn’t exist. It does. The problem is that most global databases are not calibrated for GCC conditions — they often overlook local construction methods, material sourcing, labour rates, and climate impact.
Solution: Leverage tools such as One Click LCA with GCC-specific datasets. Refer to methodologies by the Global Carbon Council to ensure emissions data aligns with regional standards. More importantly, engage regional cost consultants and sustainability experts to localise assumptions and align results with current market realities.
2. The barrier isn’t tools, it’s the capability and confidence
Across project teams, the appetite for sustainable design and LCCA is high. What’s lacking is structured know-how. Too often, sustainability and cost decisions are handled in isolation due to a gap in technical familiarity.
Solution: Begin with structured templates and intuitive LCCA software. Build internal capability through training, or upskill via LEED, Estidama, and BREEAM pathways. Developing in-house fluency doesn’t require large investment, but it does require intent.
3. Capital cost pushback is a framing issue, it’s not a financial one
Clients often resist sustainable alternatives because they only see the upfront price tag. What’s missing is the visibility into what that spend returns over time.
Solution: Present lifecycle cost and carbon data side by side. Use comparative visuals to reframe the conversation around value, not just expense.
4. Time pressure doesn’t excuse poor planning, it demands better timing
In the GCC, construction timelines are often accelerated. LCCA is too often introduced late, when design decisions are already locked.
Solution: Integrate LCCA from the earliest feasibility stages. That’s where it influences specifications, procurement, and sustainability outcomes most effectively.
By proactively addressing these barriers, construction professionals can unlock the full potential of LCCA. This approach reduces costs while delivering climate-aligned, future-proof assets.
Conclusion
As sustainability becomes a baseline expectation rather than a bonus, life cycle cost analysis (LCCA) stands as one of the most powerful yet underutilised tools in the construction industry's decarbonisation toolkit. More than a budgetary measure, it is a strategic framework that transforms how we design, build, and manage the built environment.
By combining financial and environmental analysis, LCCA gives developers, designers, and investors a clear roadmap to deliver assets that are both high-performing and climate-aligned. It shifts the focus from short-term costs to long-term value, while also helping navigate regulatory demands and ESG expectations.
More than ever, the question isn’t whether you can afford to use LCCA. The real question is whether you can afford not to.
About us
At Stonehaven, we help clients reduce emissions and costs through advanced life cycle cost analysis (LCCA) and carbon planning for the built environment.
Our team of engineers, sustainability experts, and cost consultants provide life cycle cost analysis in construction tailored to your project’s goals, whether it’s achieving net-zero, securing green financing, or improving long-term operational performance.
From early design support to post-completion audits, we use leading LCCA software, carbon modelling tools to help you make confident, future-focused decisions.
Stonehaven supports clients across the UAE and wider region, specialising in commercial, infrastructure, hospitality, and residential projects. We provide accurate cost and carbon insights, expert guidance for certifications like LEED, BREEAM, and Estidama, and transparent models for investors and regulators. Every recommendation is backed by real-world examples, helping you make smart, future-focused decisions for a low-carbon built environment.