In the fast-paced world of construction, staying ahead demands efficient, adaptable logistics and supply chain management. Projects hinge on precision timing, resource availability, and collaboration between multiple stakeholders. When managed effectively, logistics and supply chain strategies can streamline processes, cut costs, and contribute to overall project success. However, challenges such as supply chain disruptions, tight budgets, and complex workflows make it imperative for construction firms to have a proactive approach to these areas.
Logistics and supply chain management in construction isn’t merely about transporting materials from A to B; it’s about designing a seamless, interconnected process that maximises productivity and reduces risk. In this blog, we’ll explore the components of logistics and supply chain management, delve into specific challenges and opportunities in construction, and provide actionable insights to help construction firms thrive.
The construction industry’s reliance on global suppliers, complex project timelines, and stringent quality standards demands a well-coordinated logistics and supply chain strategy. Effective supply chain management isn’t optional—it’s essential to meeting deadlines, controlling costs, and ensuring quality.
What is Logistics and Supply Chain Management in Construction?
At its core, logistics and supply chain management (SCM) in construction involves the planning, execution, and oversight of supply-related activities. This includes the movement and storage of materials, equipment, and labour resources, ensuring that they reach the job site when and where needed. Unlike traditional industries, construction requires SCM solutions that account for fluctuating demands, high-value resources, and complex project specifications.
A typical construction supply chain involves the sourcing of raw materials, partnerships with logistics providers, warehousing, and on-site delivery. Each phase needs careful coordination to prevent costly delays and resource wastage.
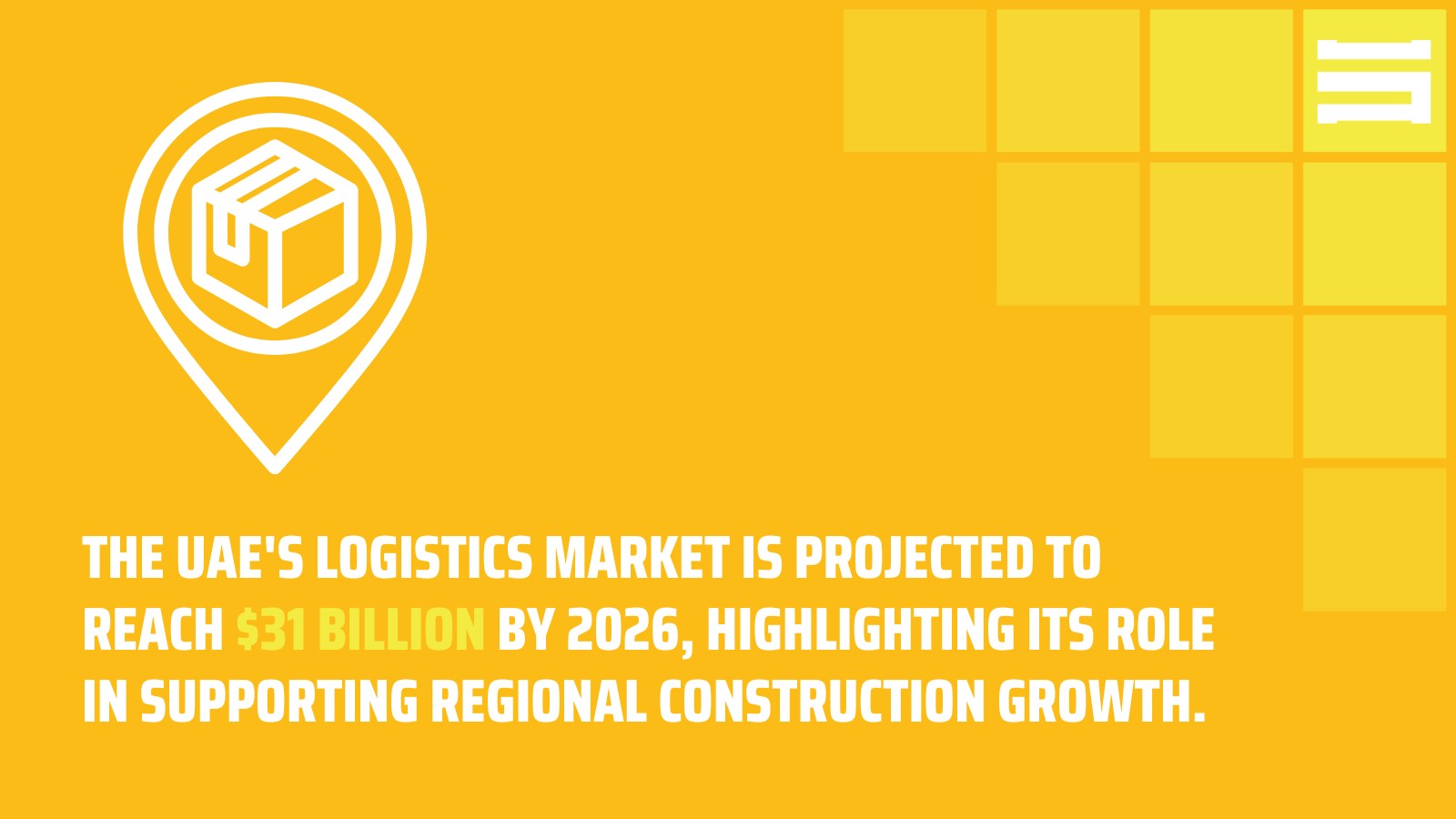
What are the Benefits of Having a Strong Supply Chain Management for Construction Projects?
The Middle East logistics sector is experiencing a growth rate that aligns with the region's strategic position, with the UAE’s logistics market projected to reach $31 billion by 2026, underscoring the importance of logistics as a core enabler for regional construction growth.
An optimised supply chain strategy in construction brings a wealth of benefits. Here are some of the primary advantages:
- Cost Efficiency
Effective logistics management minimises delays, which, in turn, reduces idle labour costs and equipment downtime. By consolidating orders, securing bulk discounts, and optimising transportation routes, firms can significantly cut down material costs. - Project Timeliness
Construction projects have strict deadlines, and even minor delays can result in penalties. SCM ensures that materials arrive just-in-time, keeping the project on schedule and preventing budget overruns. - Risk Reduction
Construction involves multiple risks—from supply chain disruptions to unforeseen delays. With an agile logistics framework, companies can adapt to challenges like price fluctuations, material shortages, or delays in a way that maintains project stability. - Sustainability Focus
A proactive logistics approach can reduce waste, optimise fuel consumption, and lower the project’s carbon footprint. Sustainability not only contributes to corporate social responsibility goals but also appeals to clients seeking eco-friendly solutions.
What are the Common Approaches to Logistics and Supply Chain in Construction?
To leverage the full potential of supply chain management, construction firms should adopt a strategic, flexible approach. Here are key methodologies that top SCM companies employ:
- Just-in-Time (JIT) Delivery
A JIT system aligns supply arrivals closely with project timelines, minimising on-site storage needs and reducing excess inventory. While JIT can cut costs, it also requires careful coordination with suppliers to avoid delays. - Integrated Project Management Tools
Effective logistics requires a single source of truth for managing schedules, resources, and budgets. Using digital tools like Procore firms can track real-time inventory updates, enhance communication, and simplify project management. - Supplier Relationship Management (SRM)
Strong partnerships with suppliers enhance communication and increase the chances of reliable, high-quality material sourcing. Firms should establish long-term partnerships with suppliers that demonstrate reliability and flexibility, especially under challenging conditions. - Data Analytics and Predictive Modelling
Leveraging data analytics helps predict demand, identify potential risks, and develop contingency plans. Predictive models allow construction managers to anticipate trends and avoid disruptions that could impact project outcomes. - End-to-End Visibility
From procurement to on-site delivery, visibility across the supply chain ensures that every stakeholder knows the status of materials and resources. Advanced tracking technology, combined with robust communication systems, helps avoid misunderstandings and improves accountability.
The Most Common Challenges in Construction Logistics and Supply Chain Management
While the benefits of an efficient logistics and supply chain management (SCM) system in construction are clear, the industry faces unique challenges that can significantly hinder project outcomes. Understanding these obstacles is crucial for firms aiming to implement resilient SCM strategies and maintain smooth project execution. Key obstacles include:
Facing Supply Chain Disruptions
External disruptions pose one of the greatest challenges to the construction supply chain. Global economic shifts, geopolitical tensions, and natural disasters can create sudden raw material shortages and logistics bottlenecks. A prime example was the COVID-19 pandemic, which exposed vulnerabilities in global supply chains. Construction projects worldwide were delayed as materials and skilled labour became scarce, highlighting the need for resilient and adaptable supply chains.
Additionally, unpredictable events such as the blockage of the Suez Canal and extreme weather conditions can disrupt critical shipping routes, leaving projects stalled. To combat these issues, construction firms need to have contingency planning, diversified sourcing strategies, and robust communication with suppliers. Building a resilient supply chain capable of weathering these disruptions is essential for meeting project deadlines and budget goals.
Inability to Meet Complex Regulatory Requirements
Construction logistics is bound by a stringent web of safety, environmental, and labour regulations. Firms must comply with local, national, and even international standards governing everything from material sourcing to worker safety protocols and waste disposal. The complexity grows further for projects that span multiple countries, each with its own set of regulations.
Ensuring adherence to these regulations without compromising on project timelines or budgets requires dedicated resources and continuous monitoring. Additionally, construction firms are increasingly facing pressure to meet sustainability and carbon emission standards, further complicating the logistics planning process. Non-compliance can result in severe penalties, delays, and reputational damage, underscoring the need for compliance-focused logistics management within SCM.
Constantly Fluctuating Material Costs
The cost of raw materials—steel, cement, lumber, and fuel—often fluctuates due to market demand, tariffs, transportation expenses, or unexpected supply constraints. Such price volatility is particularly challenging in the construction industry, where projects can extend over months or even years. Budget estimates set at the project’s outset can quickly become obsolete, causing financial strain and requiring unplanned adjustments.
Construction materials like concrete and steel are seeing increases around 5-6% annually, driven largely by ongoing infrastructure projects and the region's strong economic outlook, especially in Saudi Arabia and the UAE. Concrete, for example, has experienced persistent price increases due to elevated production costs and high demand across GCC countries, despite a slowdown in residential demand in certain areas.

To navigate this uncertainty, construction firms must adopt flexible budgeting practices, establish supplier contracts with price-lock agreements, and explore alternative materials where feasible. Additionally, employing predictive analytics can help forecast potential price surges, allowing for better cost management.
Limited Availability to Skilled Labour
The construction industry is grappling with a skilled labour shortage, especially as demand surges in regions with booming construction markets. Labour shortages result in project delays, increased wages, and the need for extensive workforce management. Even when skilled labour is available, it may not align with project timelines, further complicating resource allocation and project scheduling.
Factors contributing to labour shortages include an ageing workforce, insufficient training opportunities, and competition from other industries offering more stable, high-paying positions. To address this challenge, construction firms should consider investing in workforce training programs, engaging in partnerships with technical institutions, and implementing flexible work arrangements to attract a broader range of talent. Automation, although still emerging in the construction sector, is another option for addressing specific tasks where skilled labour is scarce.
Inventory and Storage Management
One of the less obvious challenges in construction logistics is managing the storage and handling of materials. While Just-in-Time (JIT) strategies reduce the need for on-site storage, not every material can be delivered on demand, especially for larger, remote construction sites. Storing materials on-site brings additional challenges, such as theft, damage, and the need for strict inventory tracking.
Storage costs and inventory management also impact the bottom line, particularly for companies operating in urban areas with limited space. In these scenarios, construction firms need to adopt precise inventory control systems, improve tracking with technology, and potentially rely on third-party warehousing solutions for materials that cannot be delivered JIT.
Environmental Sustainability Pressures of the Region
As construction moves toward more sustainable practices, logistics and supply chain operations are also expected to comply with environmental standards. The shift toward eco-friendly materials, energy-efficient transportation, and reduced waste production is becoming an industry norm, driven by regulatory standards and client demands.
According to a survey by Willis Towers Watson (WTW), 58% of supply chain leaders in construction identified climate change and environmental risks as major factors affecting supply chain resilience. This issue is compounded by the global nature of supply chains, as construction projects increasingly rely on materials from diverse and often environmentally volatile regions, driving both risks and costs in procurement and logistics.
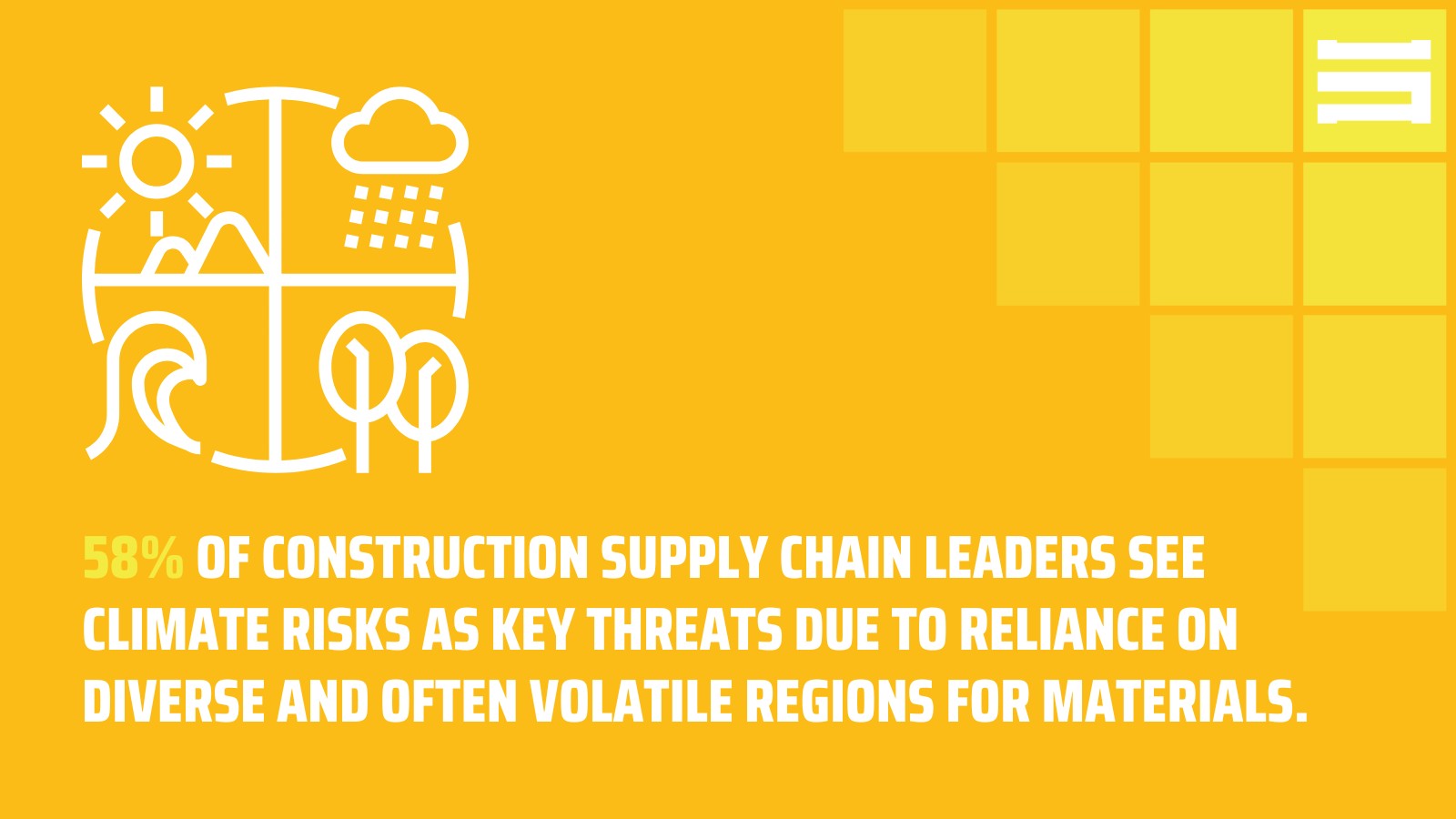
However, these sustainability requirements can strain logistics, requiring firms to source environmentally certified materials, optimise transport routes, and reduce on-site waste. For example, transporting eco-friendly materials from certified suppliers may increase costs, while choosing alternative fuel options for transport fleets requires upfront investment. Adopting green practices in construction logistics demands strategic planning and can impact project timelines and budgets, but the long-term benefits are considerable.
Technology Integration and Digital Transformation Challenges
Although technology has great potential to streamline construction logistics and SCM, implementing digital solutions comes with its own set of challenges. Integrating new technology requires training, substantial investment, and careful coordination to ensure interoperability across various platforms and devices.
Moreover, many construction firms rely on traditional methods and may lack the digital literacy needed for a full-scale digital transformation. Transitioning to technology such as IoT-enabled tracking, blockchain for transparency, and AI-driven analytics often requires a cultural shift and significant investment, both of which can be difficult to achieve. However, those that succeed in embracing digital tools stand to gain substantial improvements in efficiency, project visibility, and risk management.
What are the Opportunities in the Construction Supply Chain Landscape?
Despite these challenges, there are exciting opportunities to improve SCM in construction, including:
- Technology Adoption
Innovative technologies like Artificial Intelligence, Machine Learning, and Blockchain can revolutionise construction SCM. For example, AI-driven analytics can optimise inventory management, while Blockchain provides transparency and traceability across the supply chain. - Sustainable Supply Chains
Sustainable practices aren’t just good for the planet; they also add long-term value. Using eco-friendly materials, implementing waste-reduction strategies, and optimising transportation can improve both environmental impact and operational efficiency. - Customised SCM Solutions
Companies that invest in tailor-made SCM solutions can gain a competitive edge. By customising logistics strategies for specific projects, firms can meet unique requirements, adapt to changing project needs, and improve cost efficiency.
What are Trends Shaping the Future of Logistics and Supply Chain Management in Construction?
The construction industry is evolving, and so too is its approach to supply chain management. Key trends shaping the industry include:
- Digitalisation and Automation
From digital twins to automated warehousing, digital solutions are streamlining operations, reducing human error, and improving efficiency. As these tools become more accessible, construction SCM will continue to see increased automation. - Focus on Resilience
Recent global events have highlighted the importance of resilient supply chains. Construction firms are shifting focus toward supply chain resilience, incorporating redundancy, local sourcing, and diversified supplier bases to safeguard against disruptions. - Predictive Maintenance
Predictive maintenance tools assess equipment health in real-time, minimising downtime and repair costs. As construction projects grow in scale, managing resources proactively will be a key differentiator in project efficiency.
Conclusion
Effective logistics and supply chain management are essential for any construction project aiming to meet its objectives on time and within budget. By focusing on timely deliveries, resilient planning, and technology integration, construction firms can achieve unparalleled efficiencies and strengthen their market position. Partnering with a logistics expert like Stonehaven can streamline these efforts, allowing construction managers to focus on project execution while Stonehaven handles the complexities of SCM.
About us
Stonehaven is a leading project management company and construction consultant based in Dubai, offering comprehensive construction management services across the UAE with offices located in Dubai, UK and Sri Lanka. As one of the leading project management companies in Dubai, we manage projects from inception to completion, ensuring quality, efficiency, and cost-effectiveness at every stage.
We deliver value through expert project management consultancy services, tailored to meet the unique needs of each client. Our core services include Cost Management, Project Management, Construction Supervision, Engineering Support, Design Support, and Marketing & Communications. Whether you’re looking for construction consultants or project managers in the UAE and wider GCC region, Stonehaven is your trusted partner for achieving excellence in your next project.
We are a provider of logistics and supply chain management support, catering to the unique demands of the construction industry. Our comprehensive services include project management, supply chain analysis, and strategic planning, designed to optimise your project’s logistics and ensure consistent, reliable performance.
With a wealth of experience in the UAE and beyond, we understand the challenges and opportunities in construction SCM. Let Stonehaven support your project’s success—contact us today to learn how our expert logistics and supply chain management services can elevate your operations.