In the construction industry, change is inevitable. From unexpected site conditions to revised client requirements, change orders are a fact of life on most projects. But while some changes are unavoidable, poorly managed change orders can wreak havoc on timelines, budgets, and stakeholder trust.
That’s where effective cost management comes in. For contractors, project managers, and developers alike, handling change orders with clarity and control is essential to delivering projects on time and within budget. It isn’t just about having a signature on a document, it’s about understanding the domino effect each change may cause, how to price and document it, and most importantly, how to prevent them from derailing the project.
In this guide, we explore how to handle change orders in construction from a cost management perspective. We look at proven methods, common pitfalls, and smart tools like change order templates and flowcharts to keep you ahead of the curve. Whether you're a seasoned construction professional or just stepping into the world of project delivery, this article will help you transform change order chaos into a streamlined, documented process that protects your margins and your reputation.
How to Manage Change Orders on a Project?
Managing change orders in construction requires more than just paperwork. It demands a fully integrated system, one that is transparent, consistent, and accessible to all project stakeholders, from contractors to cost consultants. In the fast-paced world of construction project management, especially within the UAE and broader MENA region, where delays and cost overruns are common, proactive change order management can be the key to maintaining profitability.
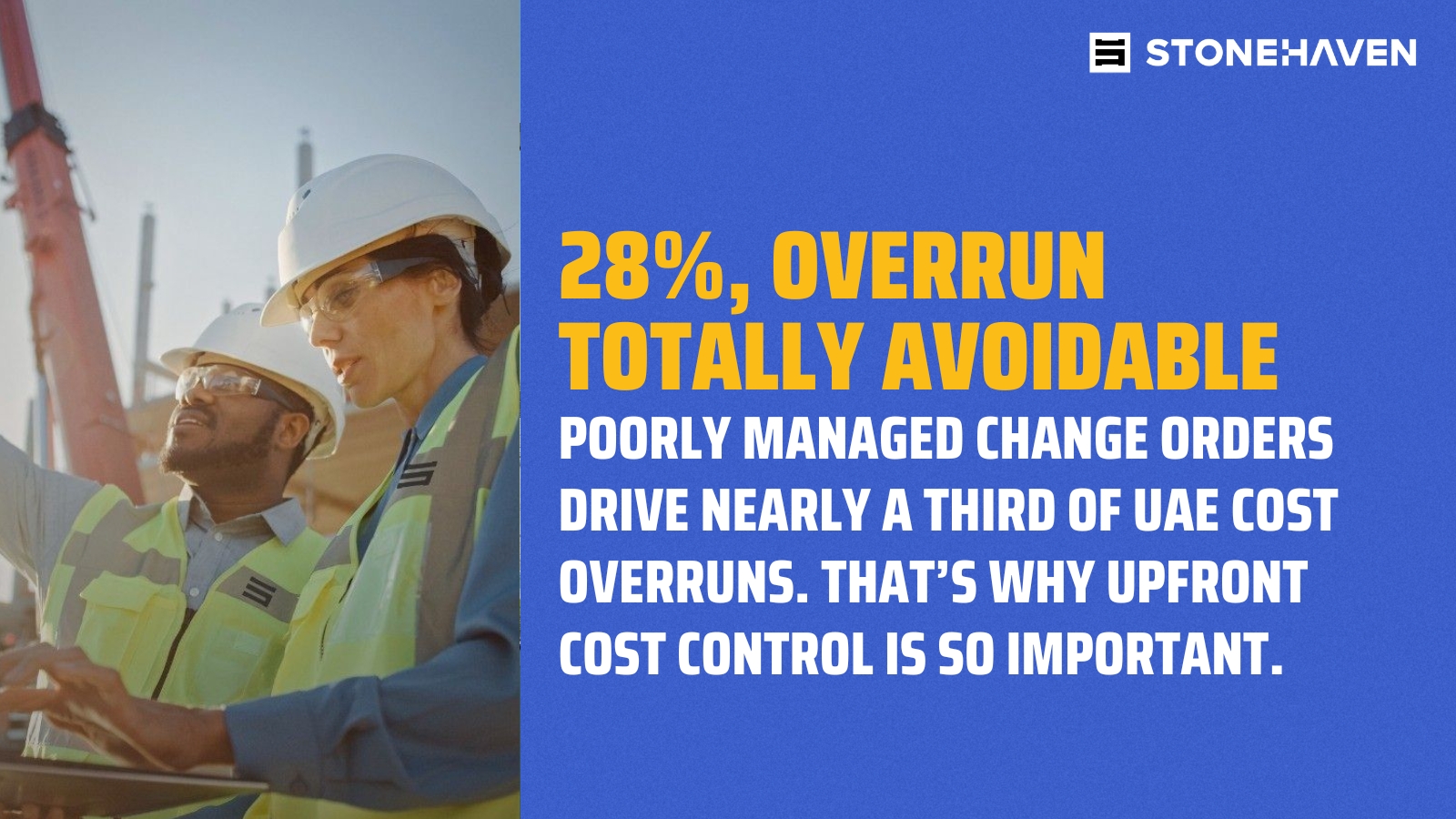
The first step is to develop a standardised change order process flowchart. This visual roadmap should clearly define when a change order is triggered, how it’s documented, who approves it, and when it’s implemented. A flowchart ensures that everyone, from the site engineer to the client, understands their role, minimising confusion and blame when plans inevitably shift.
Second, use a robust change order template. This should include detailed fields for the nature of the change, technical references (e.g. affected drawings or specifications), a cost breakdown, schedule implications, and sign-off approvals. These templates can be digitised and integrated into platforms like Procore, Oracle Aconex, or Autodesk Construction Cloud.
Third, make change orders a standing agenda item during regular project review meetings. Weekly or biweekly reviews allow the cost management team to monitor pending changes, assess impact, and maintain control. Finally, ensure early and transparent cost communication. A 2025 Middle East survey found that 28% of project cost overruns in the UAE were linked directly to poorly managed change orders. Providing early cost impact estimates, even provisional ones, can help clients understand financial implications, make faster decisions, and reduce pushback.
When implemented consistently, these practices make change orders part of the project rhythm, not disruptive anomalies. For cost managers, they offer a structured approach to preserving margins and minimising risk in an industry where scope change is the norm, not the exception.
What is the First Proper Step for a Change Order on a Project?
The first and most crucial step in handling a change order is simple in principle, but often mishandled in practice: early recognition and formal documentation. Many cost disputes and delays arise not because of the change itself, but because it was acted upon verbally, without proper records or sign-off. In a fast-moving site environment, this is a recipe for confusion, cost overruns, and strained relationships.
To begin, the project team must identify the origin of the change. Does it stem from a client-driven design revision? A response to unforeseen site conditions, such as buried utilities or contaminated soil? Or is it triggered by a change in compliance regulations or authority approvals? Categorising the source is key for tracking trends across multiple projects and improving future planning.
Once identified, a Change Order Request (COR) must be generated. Before raising a COR, the project team should review the contract to ensure the proposed change qualifies under the variation clause (e.g., FIDIC 13.1). Most standard contracts require formal written notice of a variation within a specific timeframe, most commonly 28 days. Failure to issue timely notice may result in a loss of entitlement, regardless of the validity of the claim.
This internal document is the first formal step in the change order management process. It should include:
● A clear description of the change
● The initiating party (client, contractor, consultant)
● The reason for the change (e.g., regulatory requirement, design enhancement)
● Affected scope elements, drawings, or contract packages
● A preliminary cost and time estimate, if available
At this stage, the change order process flowchart should be activated. The cost manager evaluates the request and prepares a formal change order document using a structured change order template, ensuring all necessary fields, cost breakdowns, schedule impact, supporting documents, are completed.
Next, the impact analysis begins. Cost managers and quantity surveyors calculate both direct (labour, materials, equipment) and indirect costs (programme delays, supervision hours, procurement reshuffling). This analysis supports informed decision-making before the change order moves to the client for approval. If the change affects the construction schedule, formal delay analysis techniques such as Time Impact Analysis (TIA), Windows Analysis, or As-Planned vs As-Built comparisons should be used to quantify the impact. This helps establish entitlement for extension of time and avoids future disputes.
Nothing should proceed on site without written approval. Jumping the gun creates contractual grey areas and financial risk. Once signed, the change order is logged in a centralised change order register, allowing teams to track project health and identify patterns across the lifecycle.
Embedding this as a cultural practice, not just a paperwork formality, empowers teams to stay proactive. A strong first step means fewer disputes, tighter cost control, and a smoother construction project management experience from end to end.
What is the Change Process in Construction?
In any construction project, no matter how meticulously planned, change is inevitable. Whether triggered by client-driven design alterations or unexpected site conditions, change orders are part of the day-to-day reality of project delivery. What separates successful construction companies from chaotic ones is not whether changes occur, but how they manage the change process.
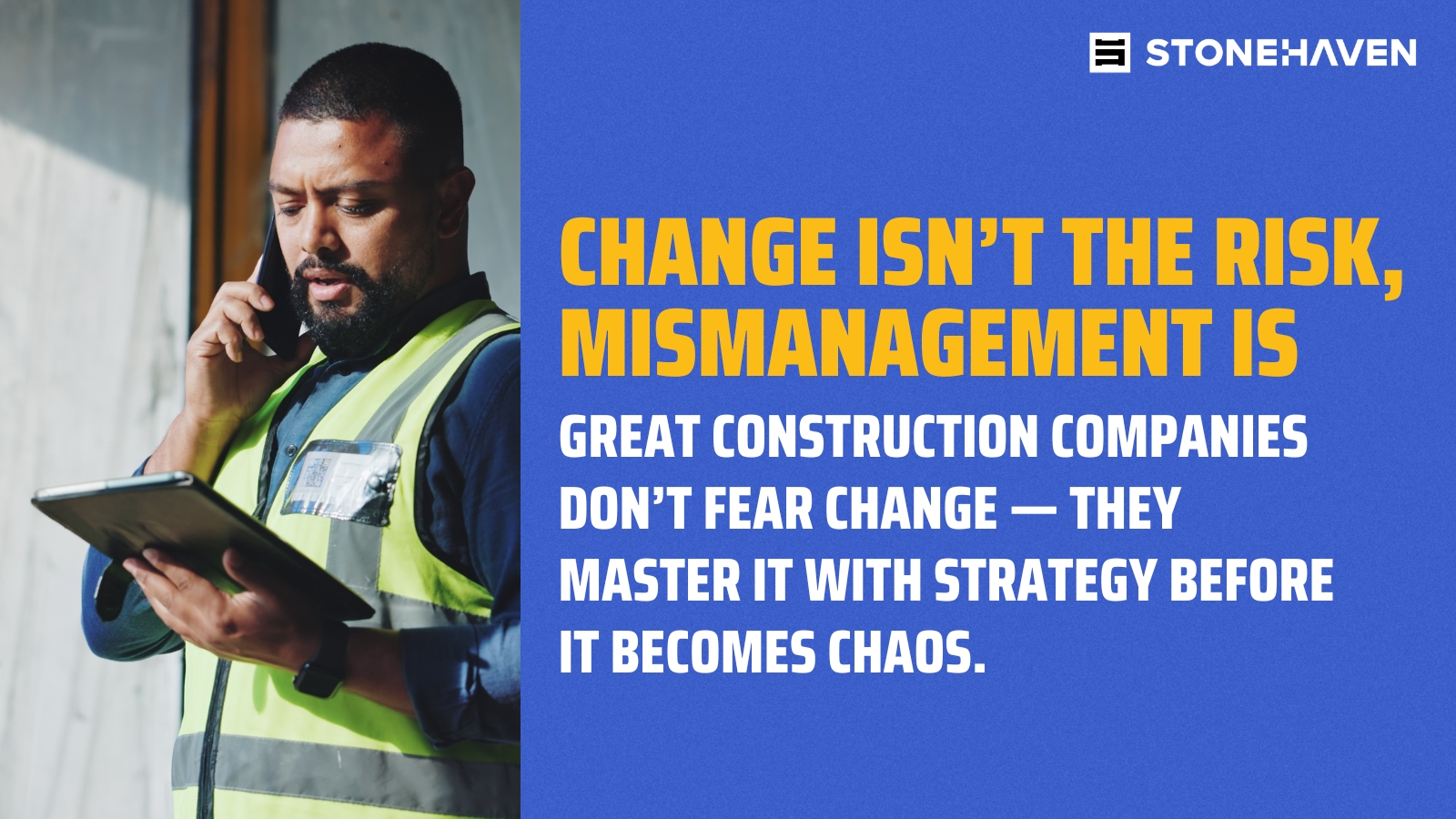
A robust change management process involves five core stages, each designed to safeguard cost, compliance, and communication:
1. Identification
The change process begins the moment a deviation from the original scope is observed or requested. This could be due to an architectural revision, a technical conflict on site, unclear contract documents, or emerging regulatory requirements. The key at this stage is early flagging. The sooner a change is identified, the easier it is to manage its cost and timeline impact.
2. Request
Once identified, a Change Order Request (COR) should be formally raised. This document, typically submitted by the contractor, subcontractor, or supervising consultant, outlines the nature of the change and its estimated consequences. This is a critical moment for clarity, ambiguities in the request often lead to disputes later. Using a change order template ensures the necessary details are captured: change description, scope impact, reason for change, and initial cost/time implications.
3. Evaluation
Next comes the evaluation phase, led by cost consultants, project managers, and engineers. They assess:
● Whether the change is contractually valid or necessary
● How it affects the project budget, schedule, and resourcing
● Compliance issues and downstream procurement or construction impacts
This is where digital tools, like a change order process flowchart, cost forecasting software, and project dashboards, become indispensable. Transparent systems speed up approvals and reduce friction across teams.
At this point, the proposed change should also be evaluated for risk implications. If significant, it should be added to the project risk register with appropriate mitigation actions. Linking change management with risk management ensures cross-functional awareness and leads to better decision-making.
4. Approval or Rejection
The formal change order, once evaluated, is submitted to the client or authorising party. It may be approved as-is, modified, or rejected. Only approved changes should proceed to execution. This stage protects both contractors and clients from miscommunication and liability.
5. Implementation and Recordkeeping
Once approved, the change is implemented on site. Progress is tracked, budget lines adjusted, and affected timelines updated. Crucially, every change should be recorded in a centralised change order register. This acts as a live audit trail, supporting accountability, benchmarking, and dispute resolution if needed.
What are the Examples of Change Orders?
Change orders in construction are as varied as the projects they affect. While they may appear as minor tweaks, their impact on cost, schedule, and scope can be substantial. Recognising the different types of change orders in construction early, and documenting them with the proper process, helps contractors and cost managers mitigate risks before they spiral into delays or disputes.
Here are some of the most common examples of change orders on construction sites across the UAE and wider MENA region:
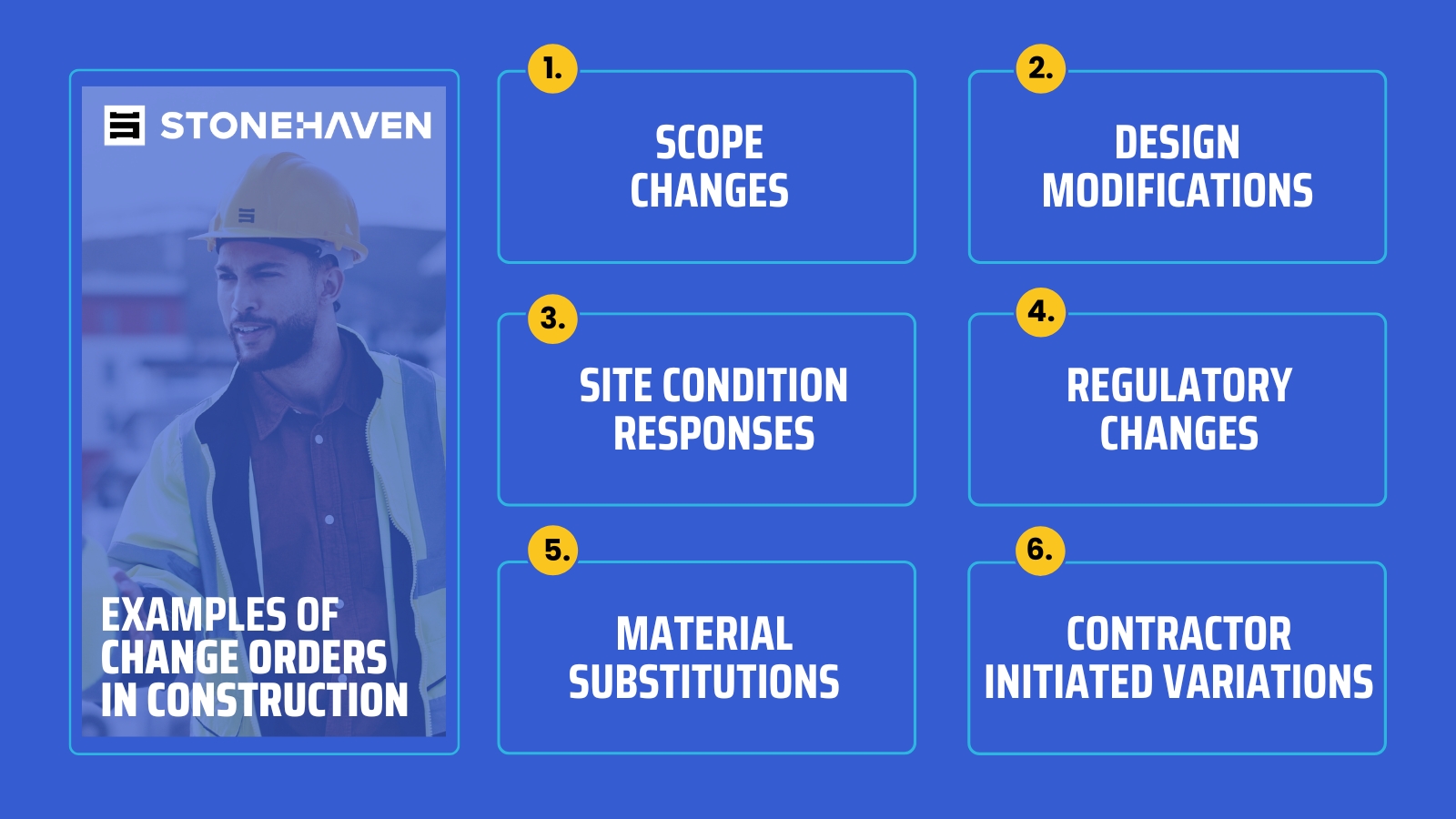
1. Scope Changes
Example: A client requests an additional floor or the expansion of the parking area mid-construction.
Impact: These changes require revisions to structural design, new permits, increased procurement, and possibly the extension of timelines and labour allocation. They’re among the most costly and time-consuming types of change orders and require detailed cost breakdowns in the change order template.
2. Design Modifications
Example: An architect revises the façade or alters window specifications after procurement is underway.
Impact: This can cause procurement delays, increase material costs, and require new installation procedures, potentially affecting the critical path of the project.
3. Site Condition Responses
Example: Excavation reveals unforeseen rock formations or underground water.
Impact: Site-specific surprises like these can significantly delay foundation work and necessitate new equipment, revised engineering calculations, and change approvals. These are especially common in MENA regions where geological assessments may be limited in urban zones.
4. Regulatory Compliance Changes
Example: Authorities revise fire safety or accessibility codes mid-project.
Impact: The project must comply, meaning design and MEP systems may need to be reworked. The change must be justified and well-documented, especially in high-rise or hospitality projects where code compliance is non-negotiable.
5. Material or Product Substitutions
Example: A selected marble tile becomes unavailable; the client approves an alternative.
Impact: This substitution might alter aesthetics, cost, and installation technique. It may also void warranties or impact sustainability certifications unless properly documented.
6. Contractor-Initiated Variations
Example: The contractor proposes a value engineering solution, such as a faster installation method or material substitution that reduces cost.
Impact: While potentially beneficial, these variations still require formal approval via the change order process flowchart to ensure accountability and contractual clarity.
Each of these examples underscores why agile but structured project management for construction projects is essential. With a change order template in place, including clear cost/time estimates and sign-offs, teams can manage these changes professionally, maintaining financial discipline while allowing for adaptive delivery in dynamic environments.
Challenges and Solutions for Managing Change Orders
While change orders are a standard part of construction project management, handling them without a structured process can lead to disputes, delays, and strained relationships. In the UAE and broader MENA construction industry, where fast-paced projects and complex stakeholder networks are common, these challenges are magnified. Below are five of the most pressing challenges cost managers face when dealing with change orders, along with practical, field-tested solutions.
Challenge 1: Delayed Approval
Delayed client approvals can grind on-site work to a halt. When site teams are uncertain whether to proceed, productivity suffers and timelines slip. These bottlenecks are particularly damaging on design-build and fit-out projects where sequencing is critical.
Solution: Incorporate fixed approval timelines into contracts, typically 3–5 business days. Escalation protocols should kick in automatically if the deadline lapses. Using cloud-based construction project management platforms ensures change order templates are visible to all decision-makers in real time.
Challenge 2: Cost Disputes
Clients often dispute cost estimates when they’re vague or not broken down into line items. This erodes trust and can delay sign-off further.
Solution: Provide transparent costing in every change order template. Break down the estimate into material, labour, plant, overheads, and mark-up. Adding comparison tables (before vs after) and impact summaries enhances clarity and professionalism.
Challenge 3: Scope Creep
Repeated informal changes, often introduced verbally or via casual emails, can bloat the project scope and budget without proper tracking. These unapproved adjustments are notorious for driving cost overruns in high-end and government-backed developments.
In lump sum or GMP contracts, pre-agreed contingency allowances can be used to absorb low-risk, low-value changes without initiating full change order procedures. This speeds up project progress while maintaining budget discipline. However, usage must still be tracked and justified.
Solution: Maintain a centralised change order log that tracks every approved and pending change. Enforce a policy that no work begins on unapproved change orders. Even “minor” variations must go through the formal review process.
Challenge 4: Communication Gaps
Misalignment between contractors, consultants, and clients creates confusion around what has actually changed. Often, key details are lost in fragmented email chains.
Solution: Use integrated platforms like Procore, PlanGrid, or Autodesk Construction Cloud to centralise communication and documentation. A shared change order process flowchart helps every stakeholder visualise where things stand.
Challenge 5: Poor Documentation
When instructions are given verbally or via ad-hoc WhatsApp messages, there's no legal protection or audit trail, leaving both the contractor and client exposed.
Solution: Standardise documentation using digital change order templates and automate version control. Every variation should be timestamped, archived, and accessible in one location.
Conclusion
Change orders are inevitable, but cost overruns aren’t. The way construction companies handle change orders defines not just project success, but long-term client relationships and business sustainability.
From the moment a change is identified to the final sign-off and implementation, each step must be managed with structure, transparency, and accountability. Standard templates, flowcharts, and change order logs are not just nice-to-haves; they are essentials in the modern cost manager’s toolkit.
Contracts, tools, and team discipline all play a role, but it starts with embedding change management into the culture of project delivery. That’s what separates reactive projects from resilient ones.
Ultimately, managing change orders isn’t about avoiding them, it’s about integrating them into your workflow in a way that supports agility without compromising control. When managed correctly, they can even become value-adding moments of project optimisation.
About Us
At Stonehaven, we specialise in helping construction teams manage change with clarity and confidence. Based in the UAE, we provide end-to-end cost management services that ensure your project stays financially sound, even when the scope shifts.
We understand that change orders are more than just paperwork. Every variation affects timelines, budgets, and stakeholder trust. That’s why we support our clients with bespoke change order templates, structured process flowcharts, and integrated digital tools that streamline project tracking and approvals.
Our consultants bring deep expertise across construction project management, contractor construction, and the wider construction industry. From initial cost planning to final account close-out, we work closely with your team to ensure every change is properly documented, priced, and justified.
Whether you're delivering a residential tower in Dubai or managing a logistics facility in Abu Dhabi, Stonehaven helps you stay in control, without slowing you down.