Mechanical, Electrical, and Plumbing (MEP) planning has become a cornerstone of both structural design and building functionality. Whether the project involves a cutting-edge hospital, a luxury residential tower, or a bustling commercial hub, effective MEP supervision is indispensable. For developers, understanding how to properly prepare a MEP plan has become essential to ensuring project success.
MEP planning goes beyond improving energy efficiency, accelerating construction schedules, and avoiding costly rework. It brings together a building’s essential systems into a single, coordinated framework. However, successful MEP planning involves much more than drawing lines in CAD or BIM software. It requires cross-disciplinary collaboration, logical sequencing, cost management, compliance with regulations, and a clear understanding of how each space will be used.
This article provides a detailed overview of MEP planning, covering its definition, key components, cost considerations, and the step-by-step preparation process. It also emphasises the vital role of effective supervision in delivering successful outcomes. By the end, you will understand how a well-executed MEP plan functions as a strategic asset, helping to manage budgets, meet project timelines, enhance operational efficiency, minimise risks, and support long-term success in today’s highly competitive construction industry.
What is a MEP Plan?
An MEP plan is a comprehensive set of drawings, documents, and schedules that outlines the Mechanical, Electrical, and Plumbing systems of a construction project. These plans serve as a detailed roadmap, showing how HVAC systems, lighting, fire alarms, electrical panels, water supply, and other essential services are arranged and connected within a building.
However, an MEP plan is much more than a technical drawing. It functions as a coordination framework that ensures all systems are designed to work in harmony, avoiding conflicts with each other and with the building’s structural and architectural elements. For example, it specifies how ductwork passes through beams, how electrical conduits are routed to avoid plumbing lines, and how fire protection systems are designed to meet safety regulations. These issues are addressed during the planning phase, well before construction begins.
In today’s construction practices, MEP plans are developed using Building Information Modelling (BIM) software, which provides 3D visualisation and facilitates coordination between different engineering disciplines. The integration of BIM into MEP planning is not just a technical upgrade — it delivers tangible project benefits. For instance, MEP contractors using BIM have reported a 25% reduction in rework and a 10% decrease in labour costs, thanks to enhanced coordination and visualisation in the planning phase.
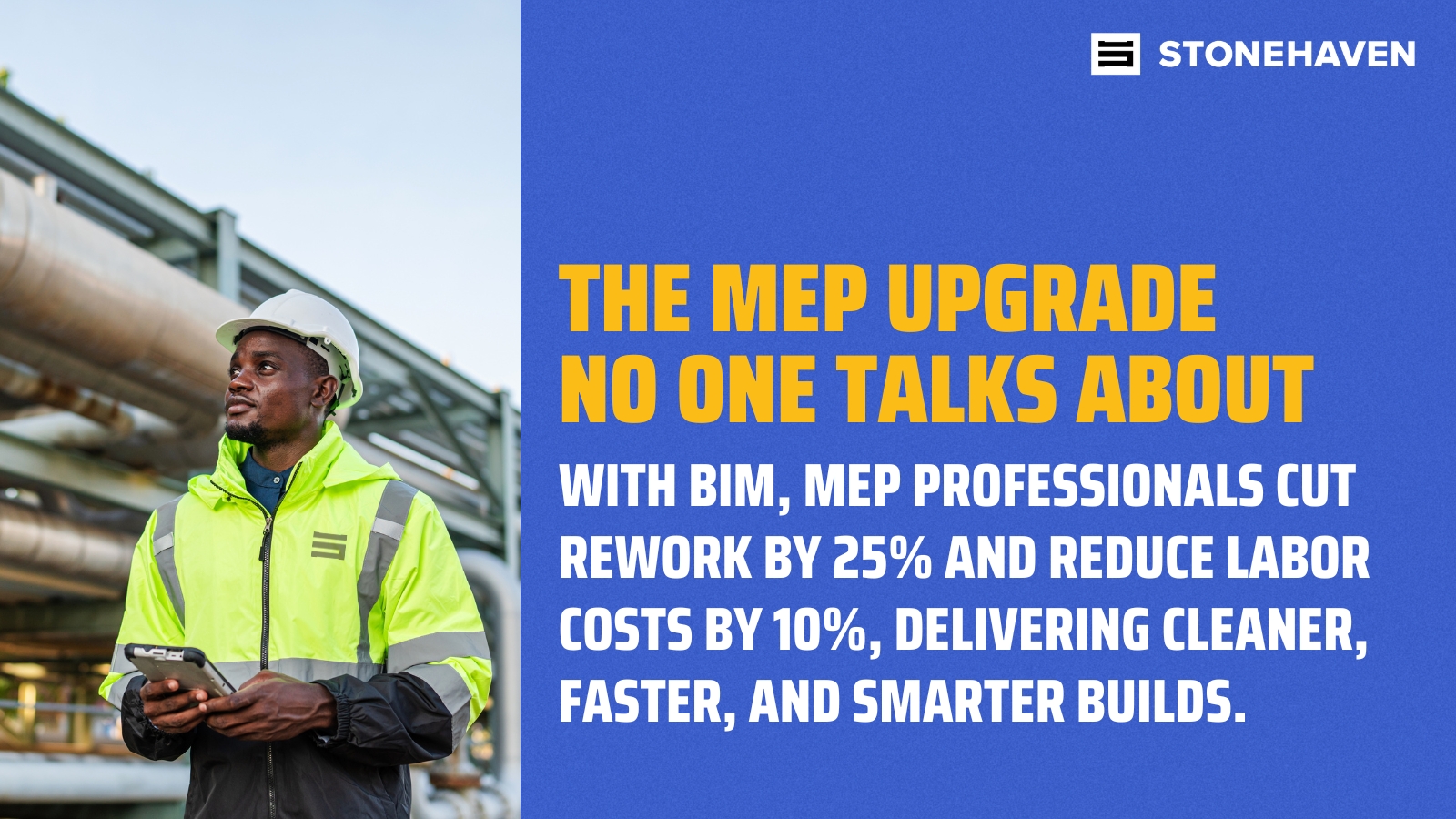
Additionally, 90% of users employing model-based prefabrication through BIM have observed improvements in quality, schedule certainty, and overall productivity compared to traditional construction methods. A properly developed MEP plan is fully integrated with architectural and structural designs, ensuring a smooth transition from planning to execution on site.
Typically, preparing an MEP plan begins with a conceptual layout and progresses to fully coordinated, construction-ready documentation. These plans undergo thorough reviews for compliance and accuracy before being approved. During construction, MEP Supervisors ensure that the design intent is accurately reflected in the final build and that on-site work aligns with project specifications.
What Role Does MEP Planning Play in Construction?
In any construction project, time, cost, and quality are the golden triangle. MEP planning sits squarely in the centre of that triangle. Without a detailed MEP strategy, even the most elegant architectural design risks functional failure.
1. Integration with Architectural and Structural Design
MEP planning begins during the design development stage, often running parallel with architectural design. The goal is integrated functionality, ensuring that systems work harmoniously with the building envelope. For example, if your architect includes high ceilings, the MEP engineer must find suitable HVAC routing that does not compromise aesthetics or performance.
2. Enabling Construction Sequencing
Think of MEP planning as the construction conductor. It guides sequencing by determining what goes in, where, and when. For instance, without proper coordination, installing a plumbing riser before finishing concrete slabs could delay timelines and increase costs. A good MEP plan anticipates and prevents these bottlenecks.
3. Budget Forecasting and Cost Control
Accurate MEP plans help project managers estimate material quantities, labour costs, and system performance over time. Using these estimates, teams can prepare realistic project plans and budgets. This also provides a foundation for cost comparisons, vendor selection, and procurement strategies.
4. Seeing Compliance and Sustainability in the Eye
Energy regulations, fire safety standards, and green building certifications all demand highly coordinated MEP systems. Whether it is BREEAM or Estidama in the UAE, compliance starts with the right MEP layout. From renewable energy integration to water conservation, all of it stems from effective early planning.
How Do You Prepare a MEP Plan for Your Project?
The preparation of a successful MEP plan requires an organised methodology and consistent collaboration between multiple stakeholders. Here's how professionals typically prepare a project plan for MEP systems:
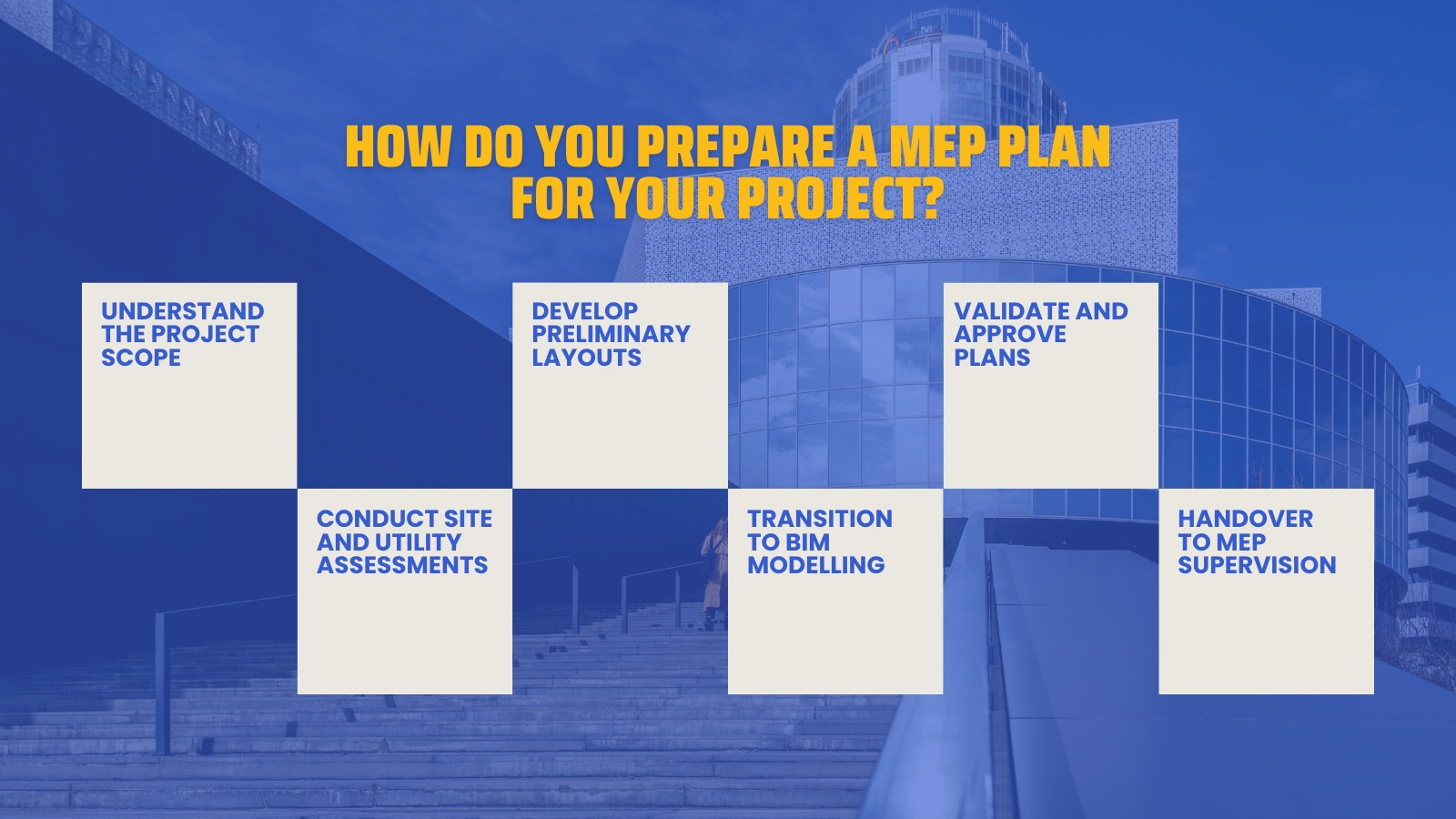
1. Understand the Project Scope
Begin by aligning with the architect, structural engineer, and client to define the building’s function, usage, and operational demands. This stage determines the MEP systems' load requirements, special needs (e.g. medical gases for hospitals), and sustainability goals.
2. Conduct Site and Utility Assessments
MEP planning is informed by existing conditions, such as soil characteristics, nearby infrastructure, and the availability of utilities. This ensures that your design aligns with real-world site constraints. Site assessments also help determine the best locations for plant rooms and the routing of MEP shafts.
3. Develop Preliminary Layouts
Preliminary 2D drawings are created, detailing HVAC zones, plumbing routes, and electrical layouts. These drawings are shared between disciplines for early feedback, minimising future rework.
4. Transition to BIM Modelling
Using BIM software allows engineers to create detailed 3D models that reflect exact dimensions, clash detection, energy modeling and systems performance simulation. These models also support prefab opportunities and digital twin applications.
5. Validate and Approve Plans
Once the design is finalised, it undergoes a thorough review to ensure compliance with building codes, safety standards, energy efficiency requirements, and coordination accuracy. The approved plans are then developed into detailed construction documents, including MEP schedules and construction sequences for implementation on site.
6. Handover to MEP Supervision
The planning phase hands the baton to supervision teams who ensure on-site work reflects the approved design. MEP supervision teams also monitor installation quality, commissioning, and system testing.
What Cost Factors Should You Consider When Preparing an MEP Plan?
When stakeholders ask, “What’s the cost of MEP planning?”, the answer is never one-size-fits-all. MEP plans cost vary based on multiple variables. Here’s what you need to know:
1. Project Size and Complexity
A small retail outlet will have vastly different MEP needs (and costs) compared to a data centre or healthcare facility. More square footage, more systems, and more specialised needs (like clean rooms) mean more detailed planning and thus higher costs.
2. Technology and Tools Used
Traditional CAD drafting is cheaper than advanced BIM modelling, but the latter offers better coordination, fewer reworks, and long-term savings.
3. Regulatory Requirements
High-rise buildings or special-use projects may require fire life safety coordination, energy modelling, and third-party approvals. These add to the planning cost but are essential for compliance and operational success.
4. MEP Plan Documentation Format
Clients and stakeholders typically require MEP plans in both PDF format for quick viewing and markup, and in native file formats like .rvt (Revit) for BIM models or .dwg (AutoCAD) for 2D drawings. Delivering layered, well-organised documentation—including schematic layouts, detailed design drawings, and coordination models, ensures all project participants (contractors, consultants, quantity surveyors, and regulatory authorities) remain aligned.
5. Cost of Revisions
MEP planning is iterative. Changes to the architectural or structural plans often lead to ripple effects in MEP layouts. Budgeting for revision cycles (typically 2–3 rounds) is smart project planning.
Investing in MEP planning is not just a line item; it's an insurance policy against future delays, claims, and compliance issues.
What Are the Advantages of Preparing an Effective MEP Plan?
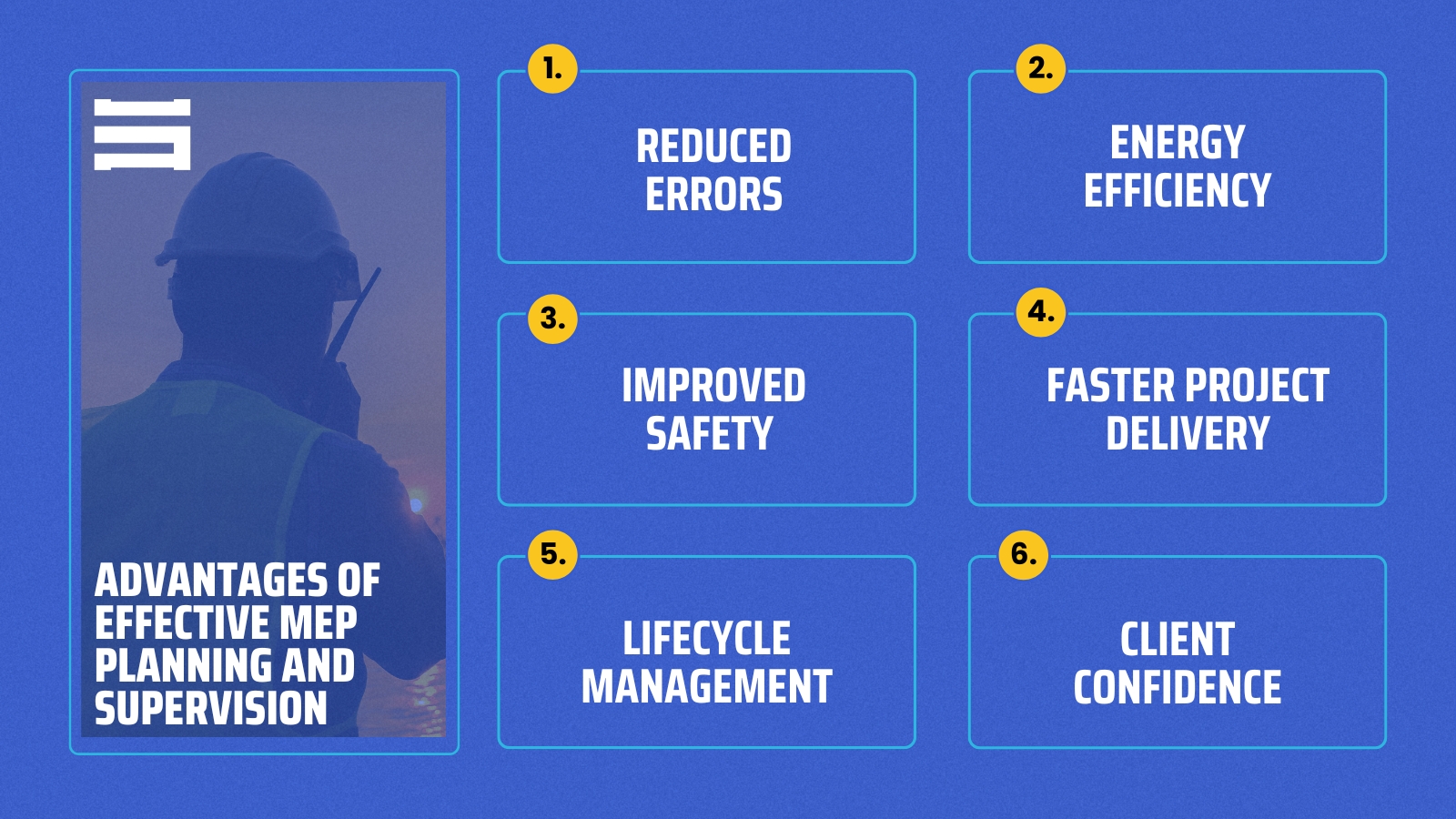
1. Reduced Construction Errors
Poor coordination between MEP systems and the building shell often leads to costly on-site clashes. Proper planning identifies and eliminates these risks before construction begins.
2. Energy Efficiency and Performance
A well-designed MEP system optimises airflow, electrical distribution, and water usage, resulting in lower utility costs and enhanced building performance. Systems designed in isolation cannot achieve this level of synergy.
3. Improved Safety and Compliance
From fire alarms to smoke exhaust and emergency lighting, MEP systems ensure life safety in emergencies. Planning ensures compliance with international and local standards from day one.
4. Faster Project Delivery
Because MEP plans define the construction sequence, they allow for off site fabrication, lean construction, and quicker installations. This shortens project duration and lowers labour costs.
5. Lifecycle Management
Modern MEP plans allow facilities managers to run building operations efficiently post-handover. BIM-enabled plans support digital twins, remote monitoring, and preventive maintenance.
6. Client Confidence
Clear MEP plans and visible supervision increase transparency, helping clients stay informed and confident that the project will meet their functional and aesthetic expectations.
How To Tackle MEP Planning Challenges
Challenge 1: Design Coordination Failures
Expanded Solution: Adopt integrated BIM processes early in the design phase, allowing all disciplines from MEP, architectural, and structural to work on a shared digital model. Mandate structured coordination meetings at every milestone and implement clash detection workflows to catch conflicts before they hit site. Assign a BIM coordinator or lead MEP consultant to oversee discipline alignment throughout the lifecycle.
Challenge 2: Frequent Scope Changes
Expanded Solution: Implement strict design phase protocols using a gated approval system. Lock major phases—concept, schematic, detailed—with formal sign-offs. Use digital change tracking tools to monitor revisions and maintain a version-controlled master MEP model. Introduce impact assessments so clients understand cost and schedule consequences of late changes before approvals.
Challenge 3: Inadequate Site Data
Expanded Solution: Go beyond basic site surveys—use ground-penetrating radar, laser scanning, and utility detection to map underground and overhead constraints accurately. Incorporate this verified data into your scanned BIM models for context-aware design. Where applicable, consult with local utility authorities early to ensure as-built records match field conditions.
Challenge 4: Budget Constraints
Expanded Solution: Value engineering isn’t about cost-cutting, it’s about smart substitutions. Conduct early workshops with stakeholders and MEP engineers to identify alternative solutions (e.g., using pre-insulated ductwork, modular electrical risers) that reduce cost without degrading system performance. Balance CAPEX and OPEX using life cycle costing (WLCC) to justify long-term ROI.
Challenge 5: Skilled Labour Shortage
Expanded Solution: Reduce dependency on site labor by increasing off-site prefabrication of MEP modules—piping racks, pump skids, risers. Use standardised assemblies to speed up installation. Simultaneously, invest in upskilling local trades through short courses on BIM interpretation, modular installation, and commissioning. Partner with trade schools or vendors to bridge skills gaps.
Challenge 6: Regulatory Delays
Expanded Solution: Involve local code consultants and authority liaison officers from the design stage. Prepare compliance checklists and regulatory trackers to pre-empt submission issues. Submit design intent drawings and system specs for early feedback from approving bodies—civil defense, utility providers, fire safety, etc. Fast-tracking approvals starts with proactive coordination.
Conclusion
A successful building does not only need to look impressive; it must function flawlessly behind the walls, ceilings, and floors. That silent, seamless operation is made possible by well-planned MEP systems. From cooling and lighting to fire safety and clean water delivery, MEP planning forms the foundation of a building's functionality.
When clients or developers inquire about how to prepare a MEP plan for a project, the answer lies in thorough preparation, precise coordination, and strong collaboration. It is not simply a checklist to complete, but an ongoing dialogue between disciplines, combining design with execution and continuous feedback throughout the process.
In today’s market, where expectations for energy efficiency, safety, and smart technologies are higher than ever, compromising on MEP design is no longer an option. Taking MEP planning seriously means committing to accurate documentation and engaging qualified supervision to ensure quality.
For any upcoming construction project, prioritising MEP planning from the outset is essential for long-term success.
About us
At Stonehaven, we ensure that every project functions as flawlessly behind the walls as it looks on the surface. Our MEP Supervision Services are designed to transform mechanical, electrical, and plumbing systems from static drawings into high-performance, fully integrated building solutions. From high-rise towers to critical healthcare facilities, we bring precision, coordination, and quality assurance to every stage of your project.
With a proven track record across the UAE and GCC, our specialist team bridges the gap between design intent and flawless execution. We challenge assumptions, verify installations, and protect your investment with hands-on expertise and meticulous attention to detail.
We ensure flawless MEP delivery through plan validation, on-site testing, BIM coordination, and strict compliance with UAE standards. Our approach includes quality audits and non-conformance management, safeguarding performance, safety, and project integrity from design to completion.
Whether you are preparing detailed MEP documentation, reviewing system architecture, or managing installation sequences, we are your trusted partner from design through to delivery.
Ensure your project performs as designed today.